Tool Steels
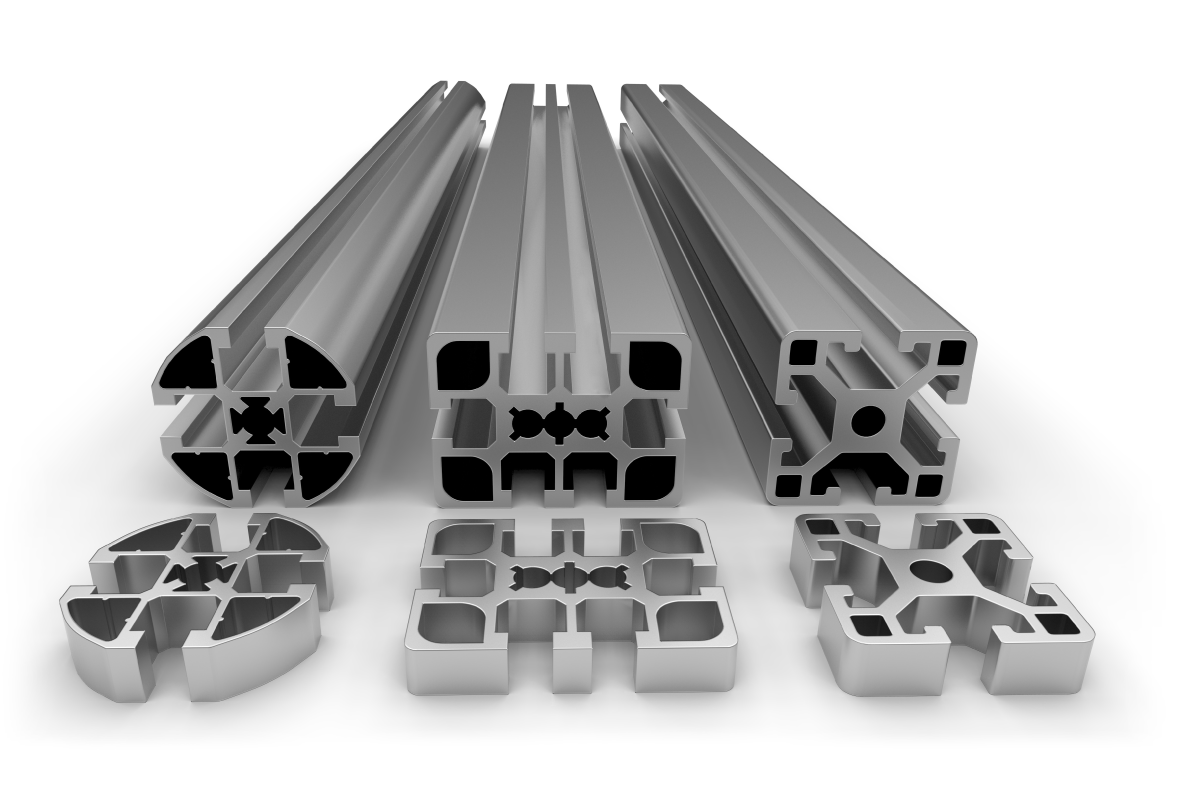
Tool and Die Steel Includes Cold Work Steel, Hot Work Steel, Plastic Mould Steel, High Speed Steel. These tool materials adhere to great quality demands of steel like temper, strength, toughness, resistance to tempering, hardening capacity, dimensional stability etc. The range of Tool Steel in our store includes products from renowned manufacturers.
Main characteristics and applications
High wear resistance hot-working steel, also be used for wear resistance and polished plastic moulds.
Steel is easy to machine in the annealed condition and needs a hardening process before final machining.
This steel also shows excellent toughness and high level insensitivity to thermal shock and thermal fatigue. A nitriding surface treatment
can be carried out to increase the life of the tooling.
Main applications:
• dies for the pressure casting of light alloys.
• wear resistance plastic moulds.
• tooling for the extrusion of light alloys and steels.
• hot work shear blades.
• rolls for profiling tools (welding area).
• Forging dies.
Hot working tools should be preheated to temperatures in the range 250 – 300°C before use.
Comparable standards
UNI | W.Nr | DIN | AFNOR | AISI/SAE | BS |
---|---|---|---|---|---|
(X40CrMoV51.1KU) | W.NR. 1.2344 | X40CrMoV5-1 | - | (H13) | (BH13) |
Chemical composition (typical; in weight %)
C | Mn | Si | Cr | Mo | P | S | V |
---|---|---|---|---|---|---|---|
0.39 | 0.4 | 1 | 5 | 1.3 | 0.015 | 0.003 | 1 |
Critical points
Ac1 860 °C
Ac3 940 °C
Ms 340 °C
Production technology
Electro-slag-remelting (ESR) - Forging – Heat treatment +EFS
US specification
In according to standard EN10228-3 Class 4 and standard SEP 1921 Class E/e
Delivery condition
WW.NR. 1.2344 is delivered in annealed condition (EFS), with hardness max 230 HB (21 HRC)
Physical properties (reference values)
20°C | 100°C | 250°C | 500°C | |
---|---|---|---|---|
Thermal expansion coefficient (10-6/K) | 11.3 | 11.6 | 12 | 13 |
Thermal conductivity (W/mk) | 18.8 | 19 | 22.9 | 25.1 |
Young modulus (Kn/mm2) | 212 | 209 | 197 | 175 |
Heat treatment
TREATMENT | TEMPERATURE | HOLDING TIME (HT) | COOLING | COMMENTS | |
---|---|---|---|---|---|
Annealing | Heat to 850 °C | Min. H.T. for 2 minute /mm | Furnace up to 550°C than in air | - | |
Stress relieving | Heat to 650-700°C | Min. H.T. for 2 minute /mm | furnace up to 300-350°C | To be carried out after machining, is recommended to eliminate the residual stresses induced by mechanical working | |
Hardening | Preheating to 350-400°C Second preheating to 750-850°C Heat to hardening temperature to 1000-1020°C | Min. H.T. for 1 minute /mm | Air or pressure gas by vacuum | Quenched hardness 52-56HRC | |
Tempering | In the range 550 – 600°C for at least 3 h according to hardness requirements and conditions of use. Tempering must be repeated a second time at a temperature equal to or 20°C lower than the previous. Before tempering, the parts must be preheated to 200 – 300°C | Air | Usual service hardness: 44-52 HRC |
C.C.T. curve
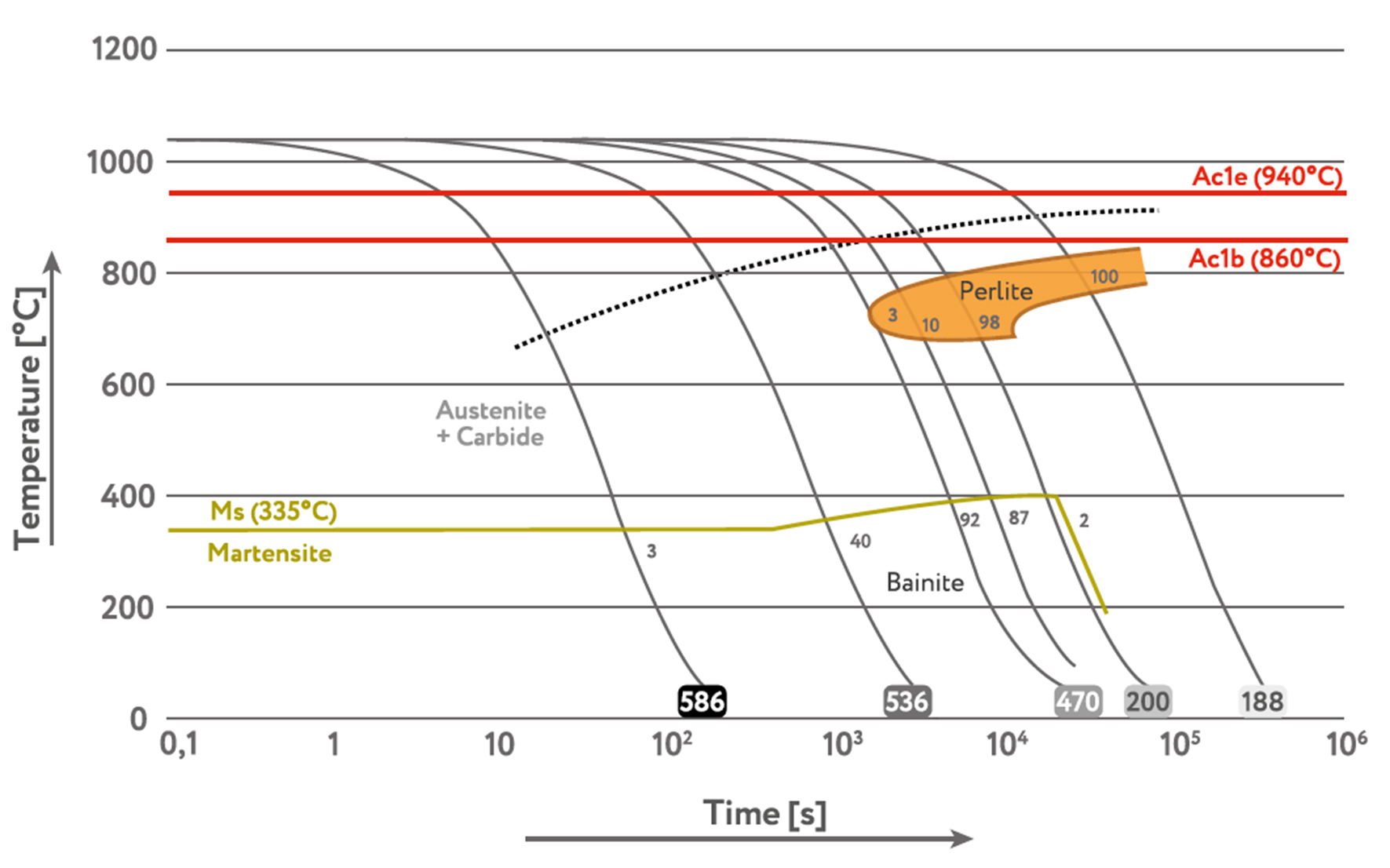
Tempering curve
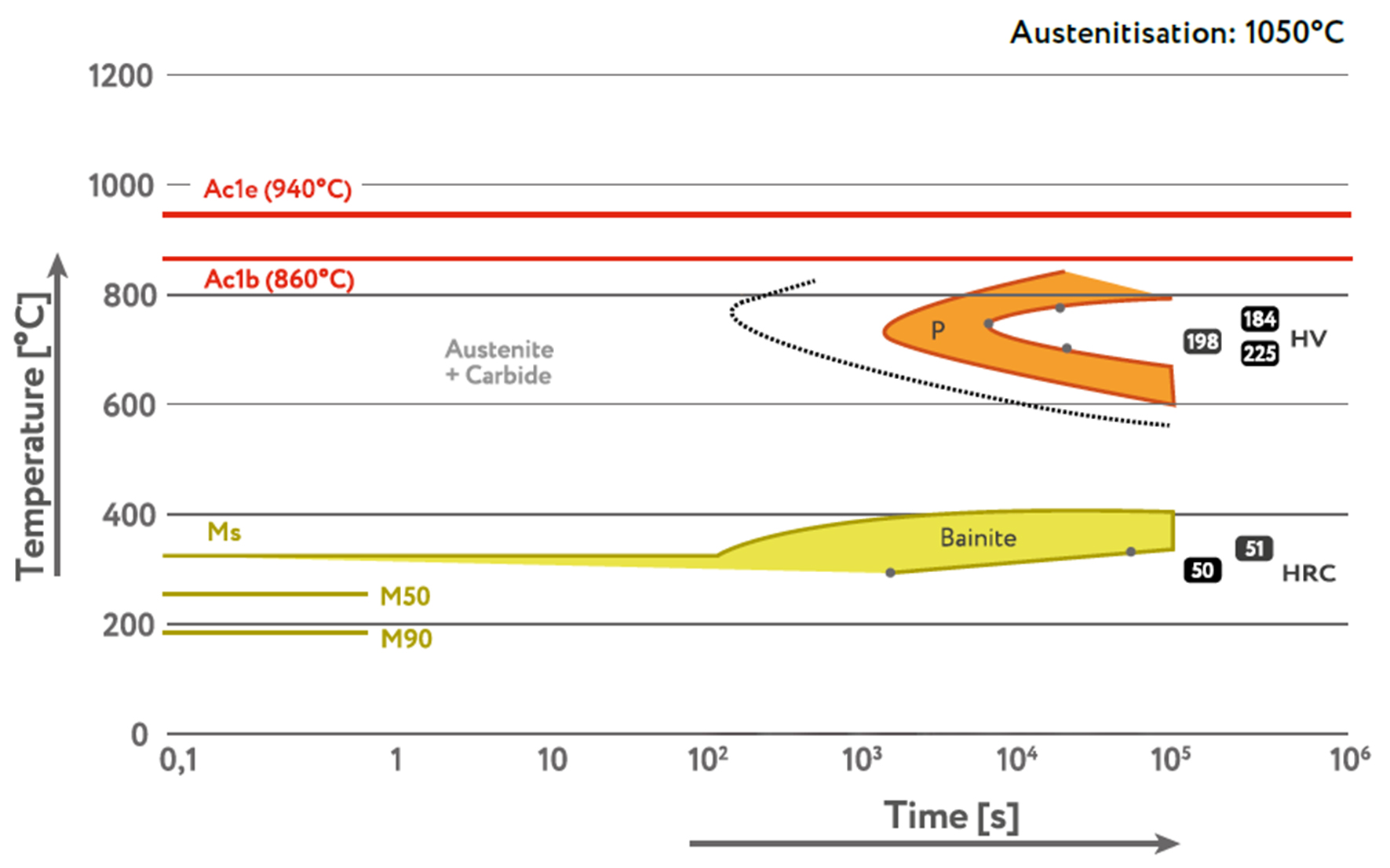